There are several more sophisticated methods for determining carbon coating thickness while carbon coating, but the color on polished brass seems to me to be a fairly direct (what about density variations?) method, considering that it relies on Newton's colors.
By the way, I suspect the main problem for some labs is the reliance on sputter carbon coaters (as opposed to actual carbon evaporation) for quantitative analysis of non-conducting samples. If you do use a carbon sputter coater for quantitative analysis, you might want to test the uniformity of your carbon coat thickness by placing a large (5 cm diameter or more), polished brass plate in your sputter coater and see how much variation you see from the center to the edge.
This is a chart that Julie Chouinard produced when she started in our lab, and it's currently laminated in plastic and posted over our Edwards 306A carbon coater:
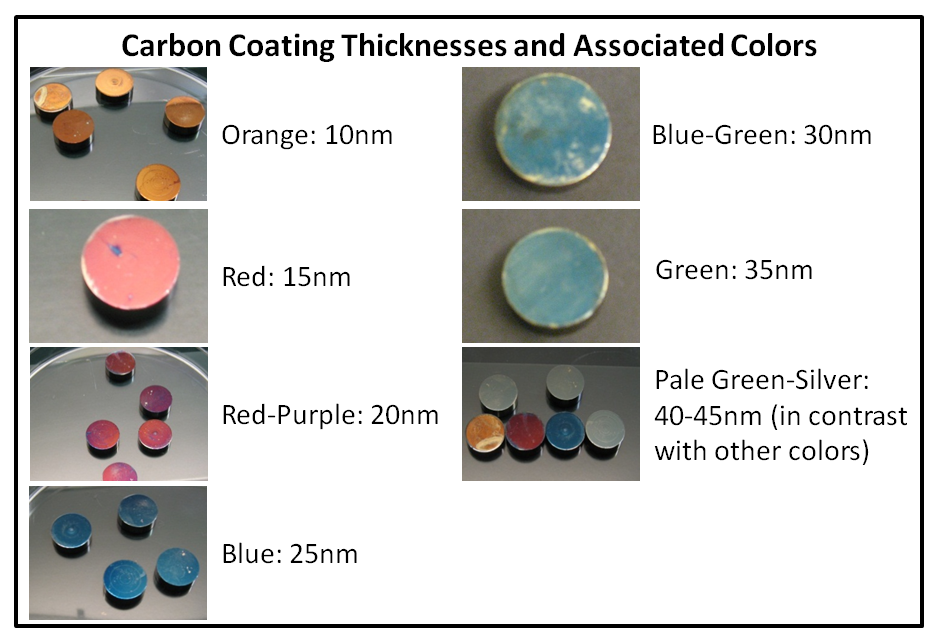
An observation: for reasonable conductivity one really only needs 10 or 15 nm of carbon (depending on the smoothness of the surface), but the transition from red to blue (at 20-25 nm) is quite striking and therefore we use this color change for thickness reproducibility.
Note that for analysis of low energy x-rays (e.g., oxygen and nitrogen Ka), one should carbon coat their standards and unknowns together at the same time.
I also attach the PowerPoint presentation of the carbon coat color document in case any one wants to modify it for their own purposes (remember to login to see attachments).