Hi Karsten
Yeah the TEM masking seemed more reproducible. I think the process of pulling the kapton off lifts the edge of the coat. To do these measurements I have to use the highest mag OBJ to get the resolution in Z I need, but this obviously limits my FOV. However I cant move far into the edge to measure thickness (where perhaps its more accurate), as I need a baseline/bare slide in the same FOV.
The masking still has/had its problems though. Below is a screen capture of a measurement from the 5x Coat
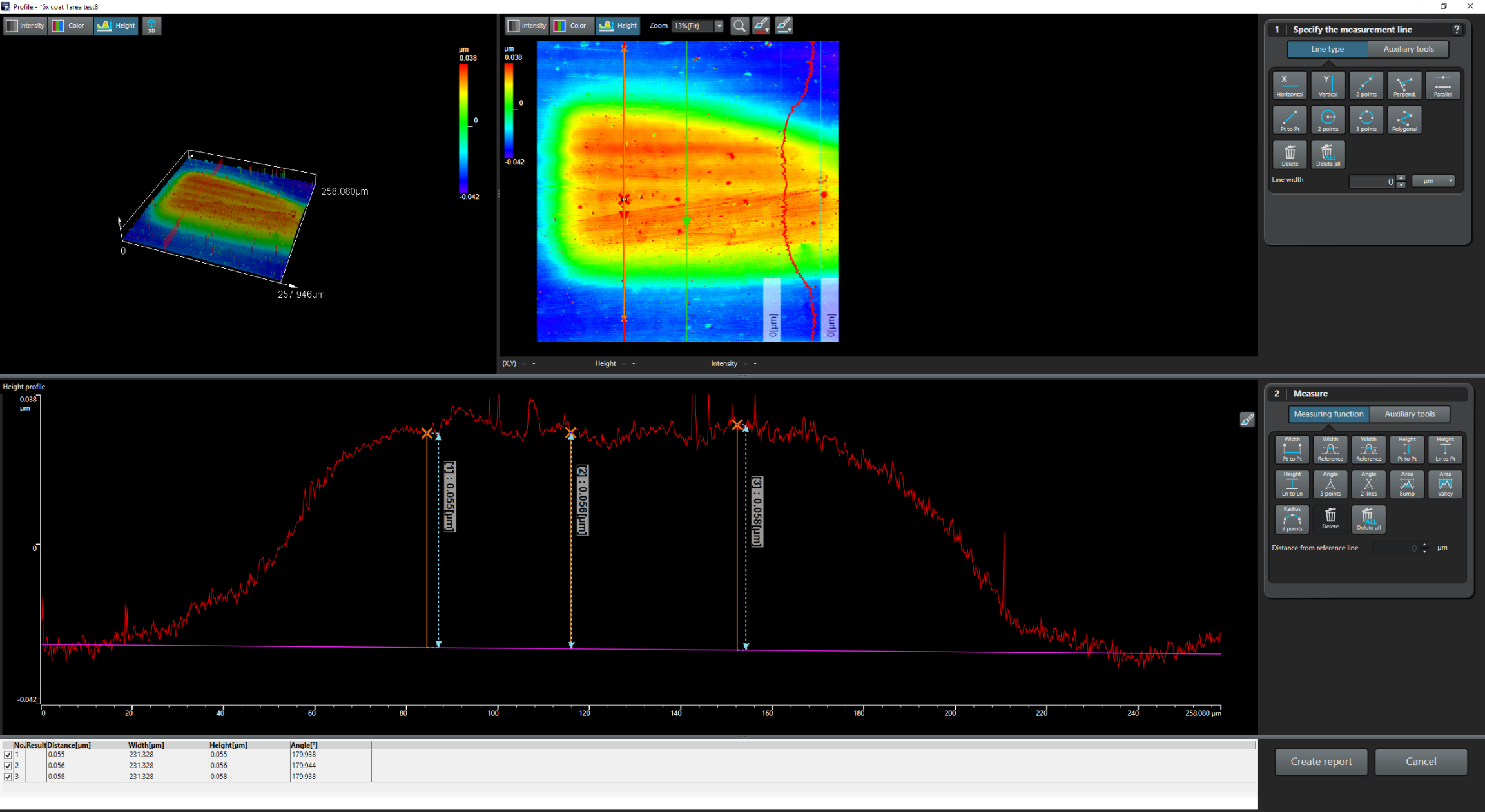
You can see the edges are obviously not sharp but a gradient, which I think is probably due to carbon bleeding/getting underneath the grid bars. Not a huge issue with the 5x coat as its so thick it reaches a plateau, but when you look at the 1x coat its not as clear cut and is much noisier. I held my grids down with strips of carbon tape, not sure how you could get around this as no matter how you hold them down they still wont lay perfectly flat and carbon will get underneath.
As you can probably tell from the image, the measurement shown above is from one of the edges of the grid, which I had to do so I could get baseline on both sides of the coat. With my 50x OBJ I cannot fit an entire "square" with baseline gridbars in the same FOV so had to resort to these edges. If I did it again I would probably use a 100 mesh grid so I could fit entire squares into the same FOV.
Also its not apparent in the 5x image above, but on the 1x/2x coat there are scanning artifacts created by our profilometer which utilises a scanning laser diode. This appears as horizontal striping at a z-scale big enough to make it a pain. I think your profilometer is an optical profilometer which should be much better at measuring thin coatings than ours.
Cheers